Electric Plastic Molding: The Future of Efficient Manufacturing
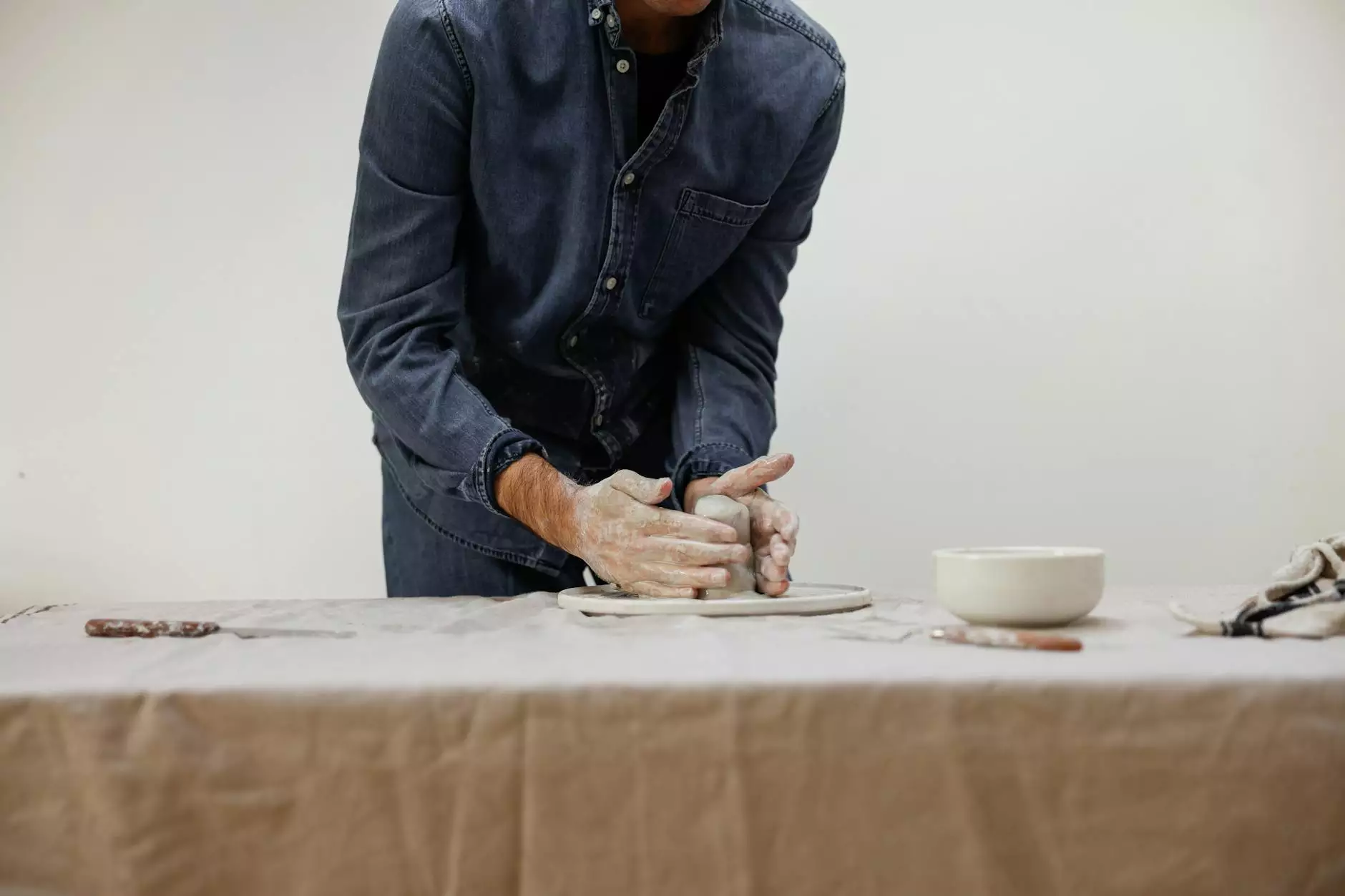
Introduction to Electric Plastic Molding
Electric Plastic Molding is a revolutionary advancement in the manufacturing industry that utilizes electric power to operate injection molding machines. This technology promises to deliver higher precision, less energy consumption, and enhanced efficiency compared to traditional hydraulic systems. As manufacturers increasingly prioritize sustainability and operational efficiency, electric plastic molding has emerged as a preferred choice for businesses looking to enhance their production processes.
Understanding the Basics of Plastic Molding
Plastic molding is a manufacturing process used to produce parts by injecting molten plastic into a mold. This method is widely used due to its ability to efficiently create complex shapes and an immense variety of products. Here are the key points to grasp about plastic molding:
- Versatility: Various plastics can be molded into desired shapes, from everyday household items to intricate components used in high-tech industries.
- Production Speed: This process allows high throughput, making it ideal for mass production.
- Cost-Effectiveness: Once the initial mold is created, the costs per unit decrease significantly as production scales.
The Advantages of Electric Plastic Molding
Electric Plastic Molding technology offers numerous advantages over traditional hydraulic methods, making it an attractive option for modern manufacturers. Below are some of the standout benefits:
1. Improved Energy Efficiency
Electric molding machines consume significantly less energy than hydraulic ones because they utilize electric motors for all motion functions. This leads to reduced operational costs and a smaller carbon footprint, aligning with global sustainability goals.
2. High Precision and Accuracy
The motion control of electric machines provides superior precision. They are capable of working with tighter tolerances, which results in higher quality parts and less material wastage. This precision is crucial in industries where exact specifications are necessary, such as automotive and aerospace.
3. Quieter Operation
Electric machines operate quietly and produce less vibration than their hydraulic counterparts, creating a better working environment and reducing noise pollution.
4. Lower Maintenance Costs
With fewer moving parts and reduced wear and tear, electric plastic molding machines require less maintenance and have a longer service life. This translates to cost savings over time for businesses.
5. Enhanced Control and Automation
Electric molding machines are commonly compatible with advanced automation technologies. Manufacturers can integrate robotics and smart systems to enhance the production process, which can lead to increased efficiency and less manual labor.
Applications of Electric Plastic Molding
The applications of Electric Plastic Molding span across various industries, demonstrating its versatility and adaptability. Here are some prominent fields utilizing this technology:
1. Automotive Industry
The automotive industry benefits significantly from electric molding as it produces high-precision parts that are fundamental to vehicle assembly. Components such as dashboards, trims, and housings are often molded using this technology to meet stringent quality standards.
2. Consumer Electronics
In consumer electronics, Electric Plastic Molding is crucial for manufacturing enclosures, buttons, and other parts that require intricate designs and high precision, supporting the ever-evolving design aesthetics of electronic devices.
3. Medical Devices
The medical sector relies on Electric Plastic Molding due to the need for clean, precise, and safe manufacturing practices. Components in medical devices, such as syringes, containers, and various housings must meet strict regulatory compliance, making the precision of electric molding machines invaluable.
4. Household Products
Simplistic yet functional household items, from containers to kitchen utensils, are easily produced with electric molding. This technology allows manufacturers to streamline production while ensuring high-quality finishes necessary for consumer satisfaction.
Challenges and Considerations
While Electric Plastic Molding brings numerous advantages, there are also challenges that manufacturers must address. Here are some key considerations:
1. Initial Investment Costs
The upfront cost of electric molding machines can be higher compared to hydraulic systems. However, the long-term savings in energy and maintenance often outweigh this initial investment.
2. Training Requirements
Employees must be trained to operate more sophisticated machinery and control systems. This requirement may necessitate additional investment in workforce development, but is ultimately beneficial.
The Future of Electric Plastic Molding
The future of Electric Plastic Molding looks promising as advancements in technology continue to shape the industry. Emerging trends to watch include:
- Integration with AI and Machine Learning: Enhanced predictive maintenance and operational efficiency.
- Greater Energy Efficiency Techniques: Ongoing efforts to reduce energy consumption in manufacturing processes.
- Expansion into New Materials: Development of electric molding methods that accommodate a wider array of plastic materials, enhancing versatility.
Conclusion
In conclusion, Electric Plastic Molding represents a transformative approach to manufacturing that emphasizes efficiency, precision, and sustainability. As businesses look to innovate and adapt in a rapidly changing market, this technology offers a myriad of benefits that cannot be overlooked. With its increasing adoption across various industries, electric molding is not just a trend; it is the future of manufacturing.
About Deep Mould
At Deep Mould, we specialize in advanced metal fabrication and plastic molding services, integrating the latest technologies to meet our clients' needs. Our expertise in Electric Plastic Molding ensures that we deliver high-quality, efficient solutions tailored to your business requirements. Explore how we can assist you in optimizing your manufacturing processes by visiting our website at deepmould.net.