CNC Lathe Turning Parts Manufacturers: Your Ultimate Guide to Precision Machining
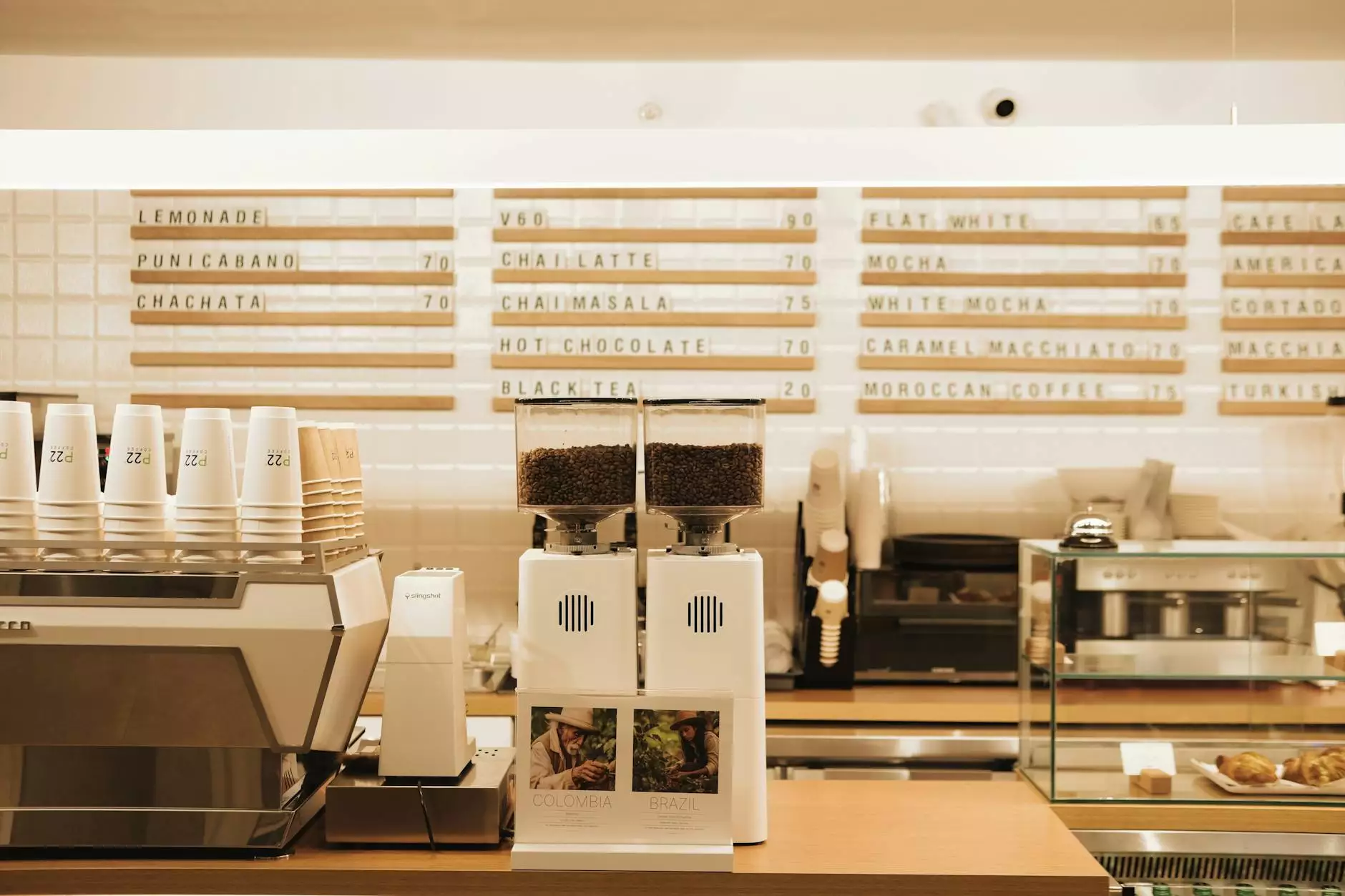
In the modern manufacturing landscape, CNC lathe turning parts manufacturers play a pivotal role in producing highly precise and intricate components essential for various industries. This article delves deep into the manufacturing process, advantages of CNC machining, and what you need to consider when choosing a manufacturer for your CNC turning parts. With the industrial evolution, these manufacturers have gained prominence by ensuring quality, efficiency, and flexibility, thus driving innovation in sectors such as automotive, aerospace, and electronics.
The Importance of CNC Lathe Turning in Manufacturing
CNC lathe turning is a critical process in metal fabrication, allowing for the production of parts that require exceptional accuracy and repeatability. Here are some essential aspects of this process:
- Precision: CNC lathes provide unmatched precision, ensuring that each part produced meets exact specifications.
- Versatility: They can work with a variety of materials including metals, plastics, and composites.
- Efficiency: Automated processes reduce manufacturing time, leading to faster delivery of products.
- Consistency: CNC machines produce uniform parts, essential for large-scale production runs.
Understanding CNC Lathe Turning Process
The CNC lathe turning process involves several steps that transform raw materials into finished products. Below is a breakdown of these critical stages:
1. Material Selection
The first step in the turning process is material selection. CNC lathe turning can utilize various metals and materials, including:
- Aluminum
- Stainless Steel
- Copper
- Plastic and Polymeric Materials
2. CAD Design and Programming
Once the material is chosen, Computer-Aided Design (CAD) software is used to create a digital blueprint of the component. This design is then converted into a format the CNC machine can interpret, typically using Computer-Aided Manufacturing (CAM) software.
3. Setup and Machining
After programming, the CNC machine is set up with the appropriate tools and fixtures. The machining process uses various tools to cut and shape the material according to the defined specifications.
4. Quality Control
As parts are produced, they undergo rigorous quality control measures. Manufacturers perform inspections using tools like micrometers and calipers to ensure dimensional accuracy and surface finish.
Benefits of Partnering with CNC Lathe Turning Parts Manufacturers
Collaborating with CNC lathe turning parts manufacturers offers numerous benefits that can enhance your production capabilities. Here are some key advantages:
1. Access to Advanced Technology
CNC manufacturers leverage the latest technologies in machining. This access to advanced machining equipment and software allows them to produce complex geometries that may be impossible with manual machining techniques.
2. Cost-effectiveness
While the initial setup for CNC machining may be higher, the long-term savings are significant due to reduced labor costs and decreased production times. This cost-effectiveness is especially noticeable in large production runs.
3. Customization
One of the greatest strengths of CNC lathe manufacturers is their ability to provide custom solutions. Whether you need standard components or highly specialized parts, these manufacturers can tailor their services to meet your specific requirements.
4. Scalability
CNC machining can easily scale production from small batches to large-scale manufacturing, making it ideal for businesses of all sizes. This scalability helps businesses respond to market changes and demands efficiently.
Choosing the Right CNC Lathe Turning Parts Manufacturer
With numerous CNC lathe turning parts manufacturers available, selecting the right partner can be a challenge. Here are some essential factors to consider:
1. Industry Experience
All manufacturers are not created equal. Look for manufacturers with extensive experience in your specific industry segment. This experience translates into a better understanding of the unique challenges and requirements you may face.
2. Quality Certifications
Ensure that the manufacturer adheres to industry quality standards and holds relevant certifications like ISO 9001. These certifications indicate a commitment to quality and consistency.
3. Technology and Capabilities
Investigate the technology they use. Advanced machines and software tools are indicative of a manufacturer’s ability to produce complex parts with precision. Confirm they have the capacity for the specific types of CNC turning required for your projects.
4. Customer Support and Communication
Assess their customer service. A responsive and communicative manufacturer can significantly enhance your project experience. Look for manufacturers that prioritize customer relationships and offer support throughout the production process.
The Future of CNC Lathe Turning Manufacturing
The field of CNC lathe turning is continuously evolving, driven by advancements in technology and innovation. Here’s what to expect in the future:
1. Integration of Automation and AI
The integration of automated systems and artificial intelligence in CNC machining can further improve efficiency and precision. These technologies promise to minimize downtime and optimize production workflows.
2. Increased Use of Composite Materials
With the rise of new materials, like composites and advanced alloys, manufacturers are likely to adapt and advance their capabilities. This means that the CNC lathe turning process will evolve to accommodate these new materials effectively.
3. Sustainability Practices
Manufacturers are increasingly adopting sustainable practices. This includes reducing waste, recycling materials, and using eco-friendly manufacturing processes. These initiatives not only help the environment but can also appeal to environmentally conscious consumers.
Conclusion
The role of CNC lathe turning parts manufacturers is vital in the landscape of modern manufacturing. As businesses strive for efficiency and precision, partnering with a competent CNC turning parts manufacturer becomes increasingly essential. By understanding the processes involved, the benefits offered, and the criteria for selection, businesses can make informed decisions that enhance product quality and operational efficiency.
Remember, in a competitive marketplace, leveraging the advantages provided by skilled CNC manufacturers is a step toward innovation and success. Embrace the future of manufacturing by aligning with the right CNC turning partner today!