Understanding Plastic Injection Tools: A Comprehensive Guide
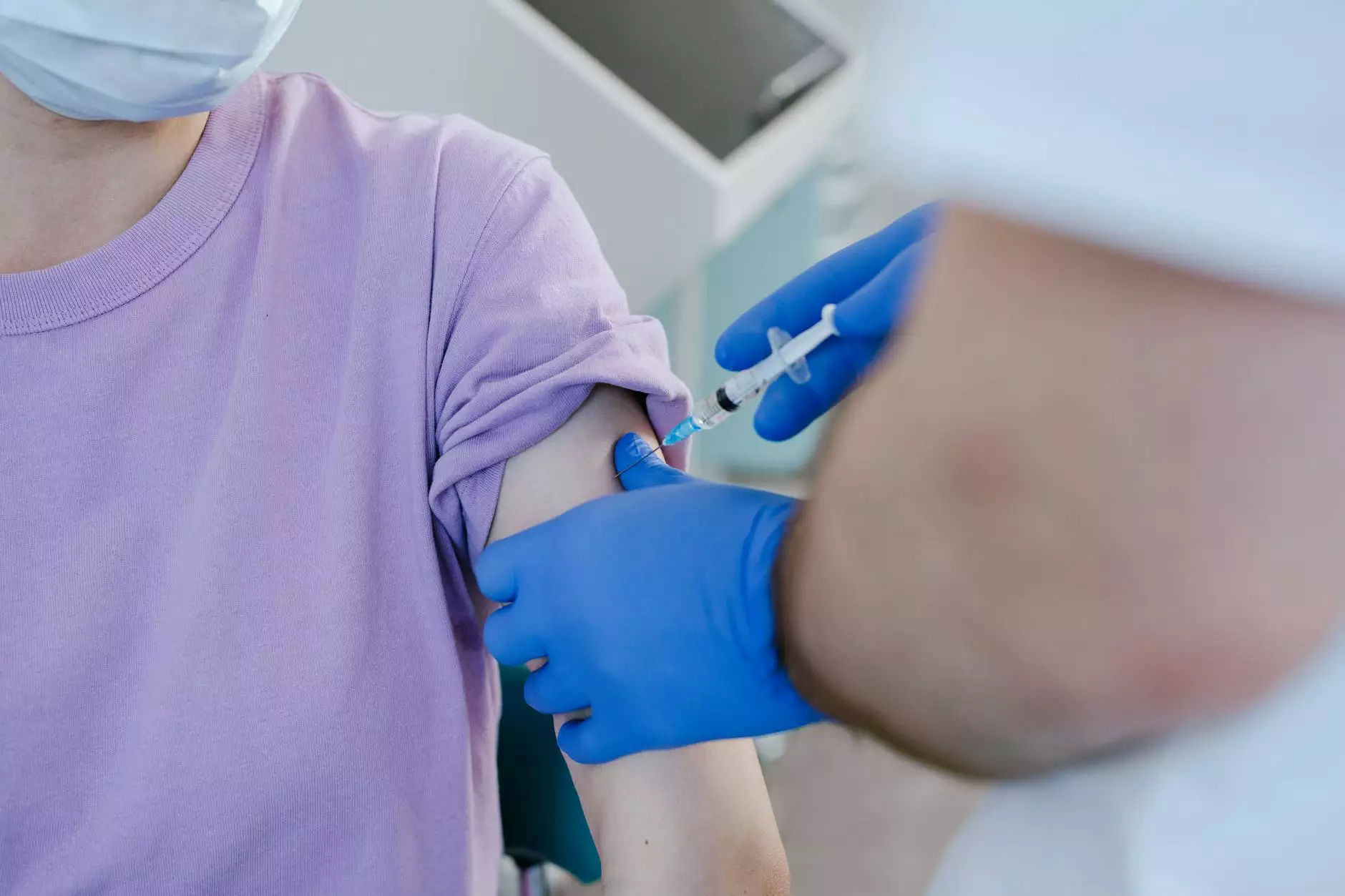
What are Plastic Injection Tools?
Plastic injection tools are essential instruments in the production of plastic parts through injection molding. This process involves melting plastic and injecting it into a mold, where it cools and solidifies into a desired shape. The efficiency and quality of molding depend largely on the precision and design of these tools.
The Importance of Plastic Injection Tools
The significance of utilizing high-quality plastic injection tools cannot be overstated. They play a critical role in various industries, including automotive, consumer goods, electronics, and medical devices. Here are several reasons why these tools are fundamental:
- Quality Assurance: High-quality tools ensure that the finished products meet stringent quality standards.
- Cost Efficiency: By reducing waste and production time, plastic injection tools save costs in large-scale manufacturing.
- Versatility: They can be designed for a diverse range of products, accommodating different plastic types and designs.
- Speed: The efficiency of the injection molding process allows for rapid production cycles, which is essential for meeting market demands.
Types of Plastic Injection Tools
When discussing plastic injection tools, various types come to mind, each designed for specific applications:
1. Single Cavity Molds
This type of mold produces one part per cycle. It is ideal for small production runs or prototype development.
2. Multi-Cavity Molds
Multi-cavity molds can produce several parts in one cycle, significantly increasing production speed and efficiency. They are perfect for larger production volumes.
3. Family Molds
Family molds allow for the production of multiple different parts simultaneously. This is particularly useful for manufacturers producing similar items.
4. Hot Runner Molds
These molds have heating elements that keep the plastic molten as it flows through the mold, reducing waste and improving cycle time.
5. Cold Runner Molds
In cold runner systems, the plastic cools in the runner, which can lead to waste. However, they are simpler and less expensive to produce than hot runner molds.
Factors to Consider When Choosing Plastic Injection Tools
Choosing the right plastic injection tools is vital for achieving manufacturing success. Consider the following factors:
- Material Compatibility: Ensure that the mold material is suitable for the type of plastic being used.
- Design Complexity: Highly intricate designs may require more advanced molds.
- Production Volume: Determine whether single or multi-cavity molds are appropriate based on anticipated production needs.
- Maintenance Requirements: Some molds require more upkeep than others; choose based on your facility's capabilities.
The Manufacturing Process of Plastic Injection Tools
The process of creating plastic injection tools involves several stages:
- Design Phase: Initial designs are created using CAD software to ensure precision and efficiency.
- Material Selection: Choosing the right alloys and plastics that can withstand high pressures and temperatures.
- Machining: Tools are cut and shaped using CNC machines to achieve the desired specifications.
- Assembly: Various components of the mold are assembled with precision to avoid any leakage or flaws.
- Testing: After assembly, molds undergo rigorous testing to ensure they operate correctly and produce high-quality parts.
Advantages of Using Plastic Injection Tools
Employing plastic injection tools in manufacturing comes with numerous advantages:
- High Production Rates: Injection molding is one of the fastest manufacturing processes.
- Reduced Material Waste: Precise control of material usage minimizes scrap and waste.
- Consistent Quality: Each injection produces uniform parts, ensuring high quality across production runs.
- Complex Designs: Injection molds can create sophisticated designs that might be difficult with other methods.
- Continuous Production: Once molds are produced, they can run continuously with minimal human intervention.
Applications of Plastic Injection Tools
Plastic injection molding is utilized in a vast array of industries. Here are some notable applications:
1. Automotive Industry
Manufacturers use plastic injection tools to create interior components, dashboards, and other critical parts.
2. Consumer Products
Everyday products like containers, household gadgets, and toys are often produced using this technology.
3. Medical Devices
The medical industry benefits from precision-made components for devices, ensuring safety and reliability.
4. Electronics
Plastic components for electronics, including casings and connectors, are rapidly produced using injection molding.
5. Packaging
Custom packaging solutions for food, pharmaceuticals, and cosmetics can be efficiently designed and manufactured.
Future Trends in Plastic Injection Tools
The industry surrounding plastic injection tools is evolving. Here are some anticipated trends:
- Automation: Increasing use of robotics to enhance the efficiency of the injection molding process.
- Sustainable Practices: Greater emphasis on using recycled materials and reducing energy consumption.
- 3D Printing Integration: Utilizing 3D printing to prototype molds and tools, saving time and costs.
- Smart Manufacturing: Implementation of IoT technologies for predictive maintenance and improved monitoring.
Conclusion
In conclusion, plastic injection tools are an integral part of modern manufacturing processes across numerous industries. Investing in high-quality tools not only improves production efficiency but also ensures product quality. As technology advances, the evolution of these tools will continue to revolutionize the manufacturing landscape, promising even greater capabilities and sustainability.
For more insights into plastic injection molding and tools, visit DeepMould.net.